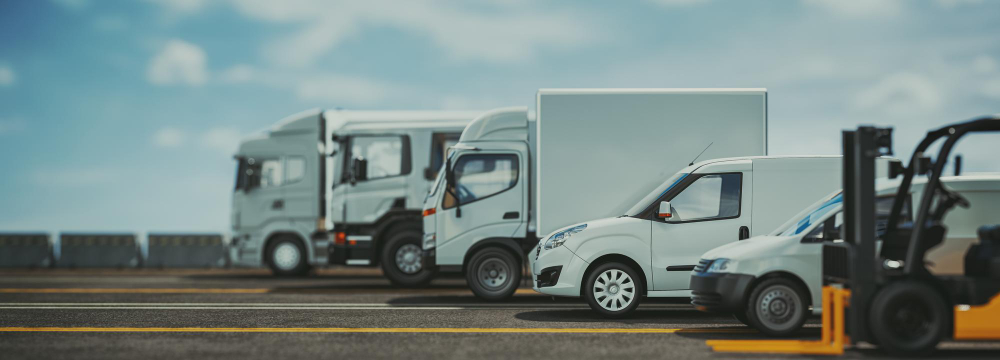
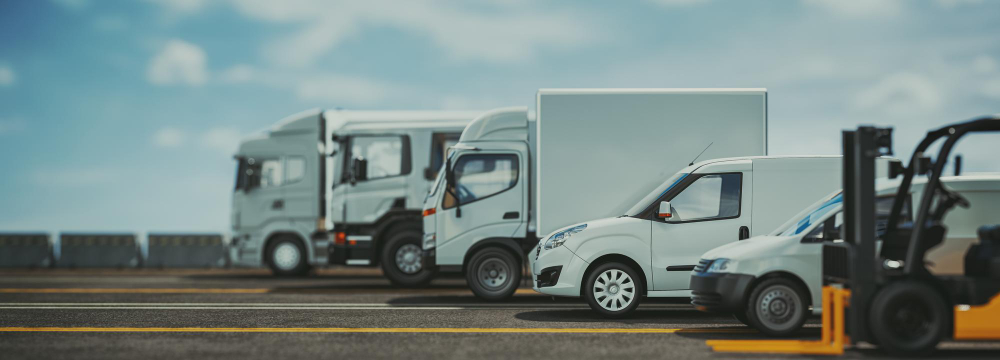
Logistyka w fabrykach: projektowanie efektywnych systemów transportu wewnętrznego
Logistyka w fabrykach odgrywa kluczową rolę w zapewnieniu płynności procesów produkcyjnych, a projektowanie efektywnych systemów transportu wewnętrznego jest jednym z najważniejszych elementów tego procesu. W niniejszym artykule omówimy, jak zaprojektować i wdrożyć skuteczne systemy transportu wewnętrznego, które przyczynią się do zwiększenia wydajności i redukcji kosztów operacyjnych.
Znaczenie logistyki wewnętrznej w fabrykach
Logistyka wewnętrzna, zwana również intralogistyką, obejmuje wszystkie procesy związane z przepływem materiałów, surowców i produktów w obrębie zakładu produkcyjnego. Efektywne zarządzanie tymi procesami jest kluczowe dla zapewnienia ciągłości produkcji, minimalizacji przestojów oraz optymalizacji kosztów. W kontekście rosnącej konkurencji na rynku, fabryki muszą nieustannie dążyć do poprawy swoich procesów logistycznych, aby utrzymać przewagę konkurencyjną.
Elementy składowe logistyki wewnętrznej
Logistyka wewnętrzna składa się z kilku kluczowych elementów, które muszą być odpowiednio zintegrowane, aby system działał sprawnie. Do najważniejszych z nich należą:
- Magazynowanie: Obejmuje zarządzanie przestrzenią magazynową, składowanie surowców, półproduktów i gotowych produktów.
- Transport wewnętrzny: Dotyczy przemieszczania materiałów i produktów pomiędzy różnymi obszarami zakładu.
- Zarządzanie zapasami: Kontrola stanów magazynowych, planowanie dostaw i optymalizacja poziomów zapasów.
- Automatyzacja procesów: Wykorzystanie technologii do automatyzacji i usprawnienia procesów logistycznych.
Projektowanie efektywnych systemów transportu wewnętrznego
Projektowanie efektywnych systemów transportu wewnętrznego wymaga uwzględnienia wielu czynników, takich jak układ zakładu, rodzaj transportowanych materiałów, dostępne technologie oraz specyficzne wymagania produkcyjne. Poniżej przedstawiamy kluczowe kroki, które należy podjąć podczas projektowania takiego systemu.
Analiza potrzeb i wymagań
Pierwszym krokiem w projektowaniu systemu transportu wewnętrznego jest dokładna analiza potrzeb i wymagań zakładu. Należy zidentyfikować wszystkie procesy produkcyjne, przepływy materiałów oraz specyficzne wymagania dotyczące transportu. Ważne jest również uwzględnienie przyszłych planów rozwoju zakładu, aby system był elastyczny i mógł być łatwo dostosowany do zmieniających się potrzeb.
Wybór odpowiednich technologii
Na rynku dostępnych jest wiele technologii transportu wewnętrznego, które mogą być wykorzystane w fabrykach. Do najpopularniejszych należą:
- Wózki widłowe: Tradycyjne rozwiązanie, które sprawdza się w wielu zakładach. Wózki widłowe są wszechstronne i mogą być wykorzystywane do transportu różnorodnych materiałów.
- Systemy przenośników: Automatyczne przenośniki taśmowe, rolkowe czy łańcuchowe, które umożliwiają ciągły transport materiałów na określonych trasach.
- AGV (Automated Guided Vehicles): Samojezdne pojazdy, które poruszają się po zakładzie zgodnie z zaprogramowanymi trasami. AGV są coraz bardziej popularne ze względu na swoją elastyczność i możliwość integracji z systemami zarządzania produkcją.
- Systemy dźwigowe: Wykorzystywane do transportu ciężkich ładunków na duże odległości lub pomiędzy różnymi poziomami zakładu.
Optymalizacja tras transportowych
Optymalizacja tras transportowych jest kluczowym elementem projektowania efektywnego systemu transportu wewnętrznego. Należy zaplanować trasy w taki sposób, aby minimalizować odległości, unikać kolizji i zatorów oraz zapewnić płynność przepływu materiałów. Warto również uwzględnić możliwość zmiany tras w zależności od aktualnych potrzeb produkcyjnych.
Integracja z systemami zarządzania produkcją
Efektywny system transportu wewnętrznego powinien być zintegrowany z systemami zarządzania produkcją, takimi jak ERP (Enterprise Resource Planning) czy MES (Manufacturing Execution System). Dzięki temu możliwe jest automatyczne planowanie i monitorowanie transportu, co przyczynia się do zwiększenia efektywności i redukcji błędów.
Szkolenie pracowników
Wdrożenie nowego systemu transportu wewnętrznego wymaga odpowiedniego przeszkolenia pracowników. Należy zapewnić im niezbędną wiedzę i umiejętności, aby mogli efektywnie korzystać z nowych technologii i procedur. Regularne szkolenia i aktualizacje wiedzy są kluczowe dla utrzymania wysokiej efektywności systemu.
Korzyści z efektywnego systemu transportu wewnętrznego
Wdrożenie efektywnego systemu transportu wewnętrznego przynosi wiele korzyści dla zakładu produkcyjnego. Do najważniejszych z nich należą:
- Zwiększenie wydajności: Optymalizacja tras i automatyzacja procesów transportowych przyczyniają się do skrócenia czasu przemieszczania materiałów i zwiększenia wydajności produkcji.
- Redukcja kosztów: Efektywny system transportu wewnętrznego pozwala na redukcję kosztów operacyjnych, takich jak koszty paliwa, utrzymania sprzętu czy wynagrodzeń pracowników.
- Poprawa bezpieczeństwa: Automatyzacja procesów transportowych i odpowiednie szkolenie pracowników przyczyniają się do zwiększenia bezpieczeństwa w zakładzie.
- Elastyczność: Nowoczesne technologie transportu wewnętrznego, takie jak AGV, pozwalają na łatwe dostosowanie systemu do zmieniających się potrzeb produkcyjnych.
- Lepsza kontrola i monitorowanie: Integracja systemu transportu wewnętrznego z systemami zarządzania produkcją umożliwia lepszą kontrolę i monitorowanie procesów logistycznych.
Przykłady wdrożeń efektywnych systemów transportu wewnętrznego
Wiele zakładów produkcyjnych na całym świecie wdrożyło efektywne systemy transportu wewnętrznego, które przyczyniły się do znacznej poprawy ich wydajności i konkurencyjności. Poniżej przedstawiamy kilka przykładów takich wdrożeń.
Przykład 1: Fabryka samochodów
W jednej z fabryk samochodów w Europie wdrożono zaawansowany system AGV do transportu komponentów pomiędzy różnymi stacjami montażowymi. Dzięki temu możliwe było zautomatyzowanie procesu dostarczania części, co przyczyniło się do skrócenia czasu montażu i zwiększenia wydajności produkcji. System AGV został zintegrowany z systemem zarządzania produkcją, co umożliwiło automatyczne planowanie tras i monitorowanie stanu zapasów.
Przykład 2: Zakład produkcji elektroniki
W zakładzie produkującym elektronikę wdrożono system przenośników taśmowych do transportu komponentów pomiędzy różnymi etapami produkcji. Przenośniki zostały zaprojektowane w taki sposób, aby minimalizować odległości i unikać kolizji. Dzięki temu możliwe było zwiększenie wydajności produkcji oraz redukcja kosztów związanych z ręcznym transportem komponentów. Dodatkowo, system przenośników został zintegrowany z systemem MES, co umożliwiło lepszą kontrolę i monitorowanie procesów produkcyjnych.
Przykład 3: Fabryka spożywcza
W fabryce spożywczej wdrożono system dźwigowy do transportu ciężkich ładunków pomiędzy różnymi poziomami zakładu. System dźwigowy został zaprojektowany w taki sposób, aby zapewnić płynność przepływu materiałów i minimalizować ryzyko uszkodzeń. Dzięki temu możliwe było zwiększenie wydajności produkcji oraz poprawa bezpieczeństwa w zakładzie. System dźwigowy został zintegrowany z systemem ERP, co umożliwiło automatyczne planowanie i monitorowanie transportu.
Podsumowanie
Projektowanie efektywnych systemów transportu wewnętrznego jest kluczowym elementem logistyki wewnętrznej w fabrykach. Wymaga to dokładnej analizy potrzeb i wymagań zakładu, wyboru odpowiednich technologii, optymalizacji tras transportowych, integracji z systemami zarządzania produkcją oraz odpowiedniego szkolenia pracowników. Wdrożenie efektywnego systemu transportu wewnętrznego przynosi wiele korzyści, takich jak zwiększenie wydajności, redukcja kosztów, poprawa bezpieczeństwa, elastyczność oraz lepsza kontrola i monitorowanie procesów logistycznych. Przykłady wdrożeń w różnych branżach pokazują, że inwestycja w nowoczesne technologie transportu wewnętrznego może przyczynić się do znacznej poprawy konkurencyjności zakładu produkcyjnego.